製品を製造するには、外部から調達する材料の購入費用(=材料費)だけでなく、購入した材料に加工を施す為の費用(=加工費)も発生します。
厳密には企業によって定義は異なりますが、加工費には、工程で製造に携わる作業者の人件費、モノの加工に用いる機械設備などの減価償却費、工場内で発生した水道光熱費、生産技術や品質管理などの製造を間接的を支援する各部門で発生した費用など、様々な費用が含まれます。
また加工費は、自社でコントロール可能な費用が多く、外部サプライヤーが関わる材料費と比較して、自社のみの努力で原価低減しやすい費用でもあります。
本日のテーマは、原価計算における加工費計算についてです。
実務における加工費計算のポイントを一緒に考えていきましょう。
材料費や間接費の計算方法については、以下をご覧頂ければと思います。
また計算方法だけでなく、原価計算の業務の概観をこちらの記事で紹介していますので、よければあわせてご覧ください。
なお計算方法に限らず、体系的に原価計算の実務について学びたい方には、こちらの書籍が大変お勧めです。
原価について初心者の方にも実務が理解し易いように纏められているので、是非チェックしてみてください。
加工費の計算方法
加工費は、製造を1時間行う毎に発生する単価と、製造時間との掛け算で計算します。
この、1時間毎に発生する単価を「チャージレート」、製造時間を「直接工数」と呼び、チャージレートは100円/hのように”1時間あたりいくら”の形で設定します。
簡単な計算例を挙げると、ある工程におけるチャージレートが100円/hで、その工程における製品A・B・Cの製造に要する直接工数がそれぞれ、10h・5h・2hの場合、製品A・B・Cの加工費は以下のようになります。
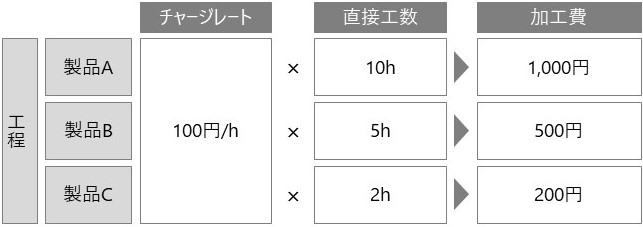
また、標準原価、実際原価ともに、加工費は「チャージレート×直接工数」で計算しますが、標準原価の計算時は「標準チャージレート×標準工数」、実際原価の計算時は「実際チャージレート×実際工数」で計算します。
(※ 実務においては、システムの制約等により実際チャージレートを計算できない場合は、実際原価の加工費を「標準チャージレート×実際工数」で計算する場合もあります)
まず、ここまでが加工費の基本的な計算方法についてでした。
それでは、このチャージレートはどのように計算するのでしょうか?
次の章では、チャージレートの計算方法を紹介します。
チャージレートの計算方法
チャージレートの前に大前提として、製品の原価は、その製品を製造する工程で発生した加工費と、その製品を構成する中間品の原価を足し合わせることで計算します。
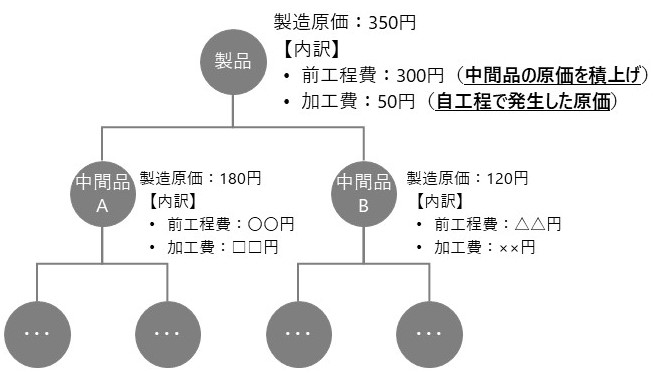
従って、原価は完成品だけでなく途中工程で生産される中間品に対しても計算しますので、チャージレートも中間品や完成品を製造する工程毎に計算します。
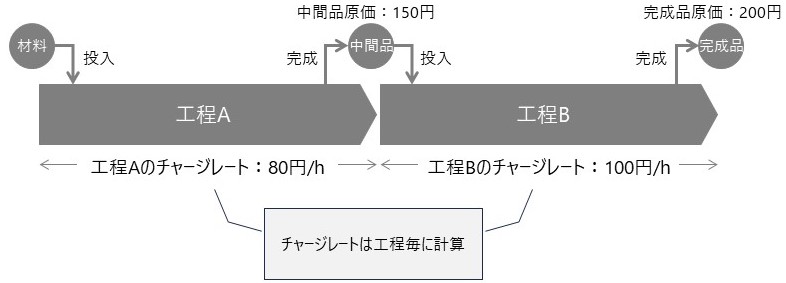
既述の通り、チャージレートは”1時間あたりいくら”という時間当たりの単価を表すため、チャージレートはその工程における加工費の合計値を、直接工数の合計値で割ることで算出します。
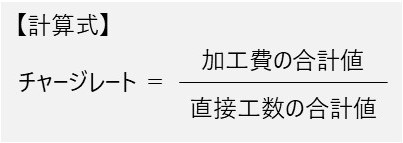
ところで、ここでは加工費のチャージレートについて言及していますが、実務では加工費よりも細かい単位で原価費目を設定し、その原価費目毎にチャージレートを算出する場合もあります。
原価費目毎にチャージレートを算出する場合も、算出方法は加工費と同様で、例えば「労務費」・「経費」の各費目のチャージレートは、その工程における労務費・経費の合計値を、直接工数の合計値で割ることで算出します。

なお、原価費目という用語が出てきましたが、原価費目については以下の記事で解説しているので、詳しく知りたい方はこちらをご覧ください。
それでは、工程における費用や直接工数の合計値はどのように算出するのでしょうか?
それぞれ見ていきましょう。
費用の合計値を算出
実務では、工程単位で管理している費用は多くなく、部や課などといった上位階層の組織単位から、各工程に費用を直課・配賦することで、工程毎に費用を集約します。
例えば、製造1課に所属する作業者の人件費を課の単位でシステムに登録している場合、その人件費は製造1課から組立工程や切削工程など、作業者が携わった工程へ直課・配賦していくイメージです。
この場合、ある工程のみの作業に従事した作業者の人件費は、その工程に直接紐づけることが可能なので、当該工程に直課します。
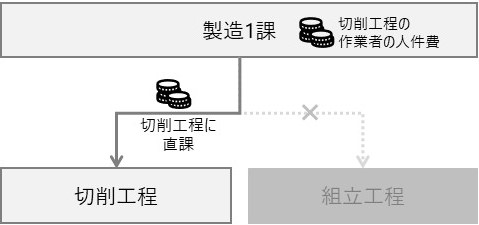
一方で、複数の工程の作業に従事した作業者の人件費は、特定の工程に紐づけることができない為、工数比率等の配賦基準を用いて、従事した各工程に配賦します。
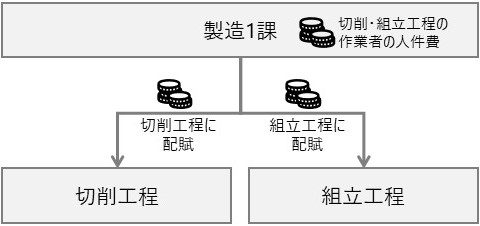
なお、上記の例では課→工程への配賦ですが、例えば部→課→係→工程のようにいくつかの段階を経て配賦する場合もあり、実務ではこのような配賦を「多段階配賦」と呼びます。
このようにして、チャージレートの計算式の分子となる費用の合計値を、各工程毎に算出します。
直接工数の合計値を算出
直接工数の合計値は、その工程で製品を1単位製造するのに要する工数(=直接工数)と、その製品の製造数の掛け算で算出します。
ただし、特定の製品を製造する専用工程でない限り、通常は各工程では複数の製品が製造され、製品毎に直接工数も製造数も異なるので、その工程で製造する各製品の「直接工数×製造数」の総和が、直接工数の合計値となります。
具体的な計算例を見てみましょう。
ある工程では、製品A・B・Cの3つの製品を製造しているとします。
これらの各製品の直接工数は、製品A:1h/個、製品B:2h/個、製品C:1.5h/個とします。
また各製品の製造数は、製品A:10個、製品B:15個、製品C:20個とします。
この場合、当該工程における直接工数の合計値は、(1h/個×10個)+(2h/個×15個)+(1.5h/個×20個)= 70hとなります。
なお、実務では直接工数の合計値を、「総直接工数」や「総直接作業時間」などと呼びます。
このようにして、チャージレートの計算式の分母となる直接工数の合計値を、各工程毎に算出します。
加工費計算における直接工数のポイント
最後に、実務上の加工費計算において、直接工数に関するポイントを2点紹介します。
ここでは概要を扱いますが、直接工数(及び間接工数)に関する具体的内容は以下の記事で紹介しているので、更に理解を深めたい場合は、あわせてご覧頂ければと思います。
マン・アワーとマシン・アワーの使い分け
工業簿記では、直接工数は「作業者などの直接工が製品を製造する時間」と学習すると思います。
それは間違っていませんが、しかし作業者の直接工数を用いて全ての加工費が計算できる程、実務は単純ではありません。
昨今は工程の自動化も進み、作業者がいなくても稼働する工程もある為、そのような工程で作業者の直接工数をもとに原価計算すると、原価の精度が低下したり、原価そのものが計算できなかったりします。
そのような場合、どうすればよいでしょうか?
1つの方法として、ヒトの作業時間であるマン・アワー(Man Hour)と、機械の稼働時間であるマシン・アワー(Machine Hour)を設け、工程毎にマン・アワーとマシン・アワーを使い分けるという方法があります。
つまり、常に作業者が張り付いている作業者主体の工程はマン・アワーを用い、作業者不在でも自動で稼働している機械主体の工程はマシン・アワーを用いて、総直接工数やチャージレート、更に加工費を計算するイメージです。
そのように、原価計算に用いる直接工数をマン・アワーとマシン・アワーで使い分けることで、原価の精度を向上できます。
直接工数の実績データが取得できない場合の対応
実際原価の計算時は、費用・直接工数ともに実績データを用いて、チャージレートや加工費を計算します。
しかし、実務では生産システムの制約等により、直接工数の実績データを取得できない場合も少なくありません。
そのような場合、どうすればよいでしょうか?
1つの方法として、直接工数は標準工数を用いて加工費を計算するという方法があります。
実際原価計算で実績データを取得できない場合は、便宜的に標準データを実績データと見做して計算することは一手となります。
なお、この場合は標準工数と実際工数との工数差による原価差異が生じますので、この原価差異はその工程で製造される各製品に適切に配賦することも必要になります。
具体的な計算方法は少々長くなるので、こちらの記事で整理しました。
よければご覧ください。
この記事で紹介する内容は以上です。
少しでも参考になれば、幸いです。